CUSTOMERS
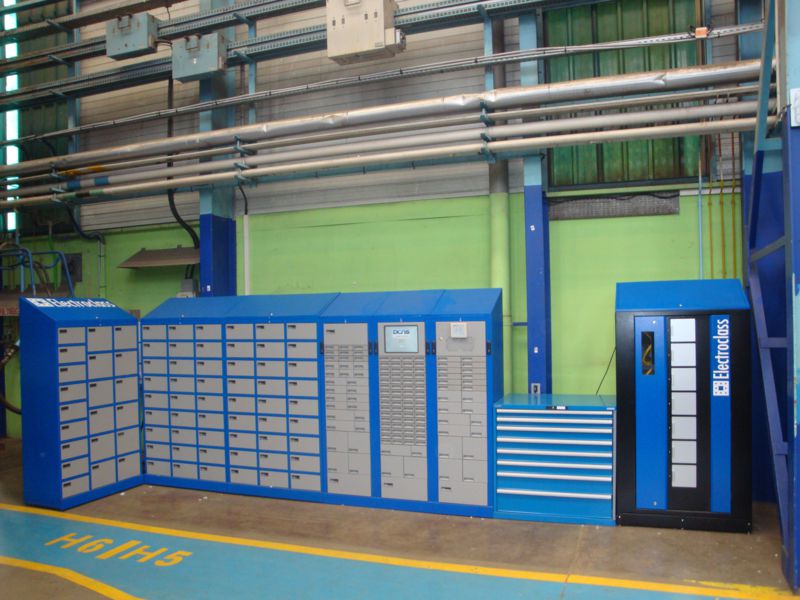
18 October 2018
Customer Presentation and Needs
Given that welding products were stored on racks in different machining shops and given that management practice meant that the welders had to jot down product inputs and outputs on a notebook, it was impossible to determine consumption with accuracy.
It was, therefore, difficult under these conditions to control the entries made and to keep track of items input and output. The welding consumables concerned by this project were highly disparate ones such as electrodes as well as an extensive range of complementary equipment.
"When the purchasing department asked us to draw up a consumption forecast for our welding over several months, we had great difficulty in quantifying the consumption."
ELECTROCLASS all-in solution
Optimizing product storage was the key element of the solution rolled out. As such, the most expensive products would benefit from per-item distribution and would be 100% secure: item-by-item, without any disparity possible. The heaviest and largest volume-sized references would be stored in tailored spaces: modules integrating doors or cabinets. The solution should lead to a reduction in consumption of between 10 and 45% depending on how the shop was managed:
- 3 SupplyPoint machines with drawers for small equipment, nozzles, piping connections, diffusers, mounts, holders, keys.
- 1 RotoPoint machine indexed to the SupplyPoint software containing filters, pre-filters, protection, spats.
- 3 LockerPoint machines with doors managing the grinding discs, flapdiscs, welding helmets, grinding helmets, coated electrodes, etc.
- 1 drawer cabinet specifically for ceramic weld backings.
"Unlike its rivals, ELECTROCLASS proposes a solution which offers warehouse/store staff the opportunity to manage vending stock autonomously."
Project results
After 3 months of testing, Mr LE MAREC commented: the test is convincing across all levels:
"There is considerable space saving and the rationing system which the solution delivers has led to a real reduction in wastage. Distribution is securely and reliably freed from time constraints. We're also seeing productivity gains, as employees' arduous toing and froing is now a thing of the past."
Warehouse/store staff are more operational at their workstation on a daily basis. The new product organization has improved and accelerated product distribution.
As regards rationalizing all the in-house movements of staff, the solution-related time gain is estimated at 25 K€.
Given this initial feedback, the project manager believes that the solution will be amortized in less than three years.
"I'm totally satisfied with the results obtained thanks to ELECTROCLASS and I've already promoted the brand to all the other Group site coordinators who have all been won over by the ELECTROCLASS system. I've sown the ELECTROCLASS seed in their minds... and I hope that the bud is going to grow…! "
Mr LE MAREC Welding Coordinator – NAVAL GROUP, Lorient site and Project Manager